Distilleries
Innovative Solutions for Spent-wash Management
Distilleries
The Alcohol Industry has been growing by leaps and bounds since the ancient ages. New times have just improved the ways and means of how these industries could be taken into rapid mode. All said and done, Distilleries remain one of the chiefs and major water and land polluting segments of the industry. The Effluent or the wastewater (termed as Spent wash) is enormously high in quantity. There have been many technological advancements done by different organizations to provide some sort of solution to the issue of Spent wash treatment, and as the preamble suggests the efforts have been half-hearted and just not enough to provide a complete ZLD to the distilleries.
Chem Process has developed a unique technology (patented) to produce high-purity salts and CMS which helps not only to resolve the problem of ZLD but also eliminate the tedious processes of Bio-composting and Incineration and in the effort of doing so, the distilleries actually start earning uncalled for profits making them self-sustainable and year-round working.
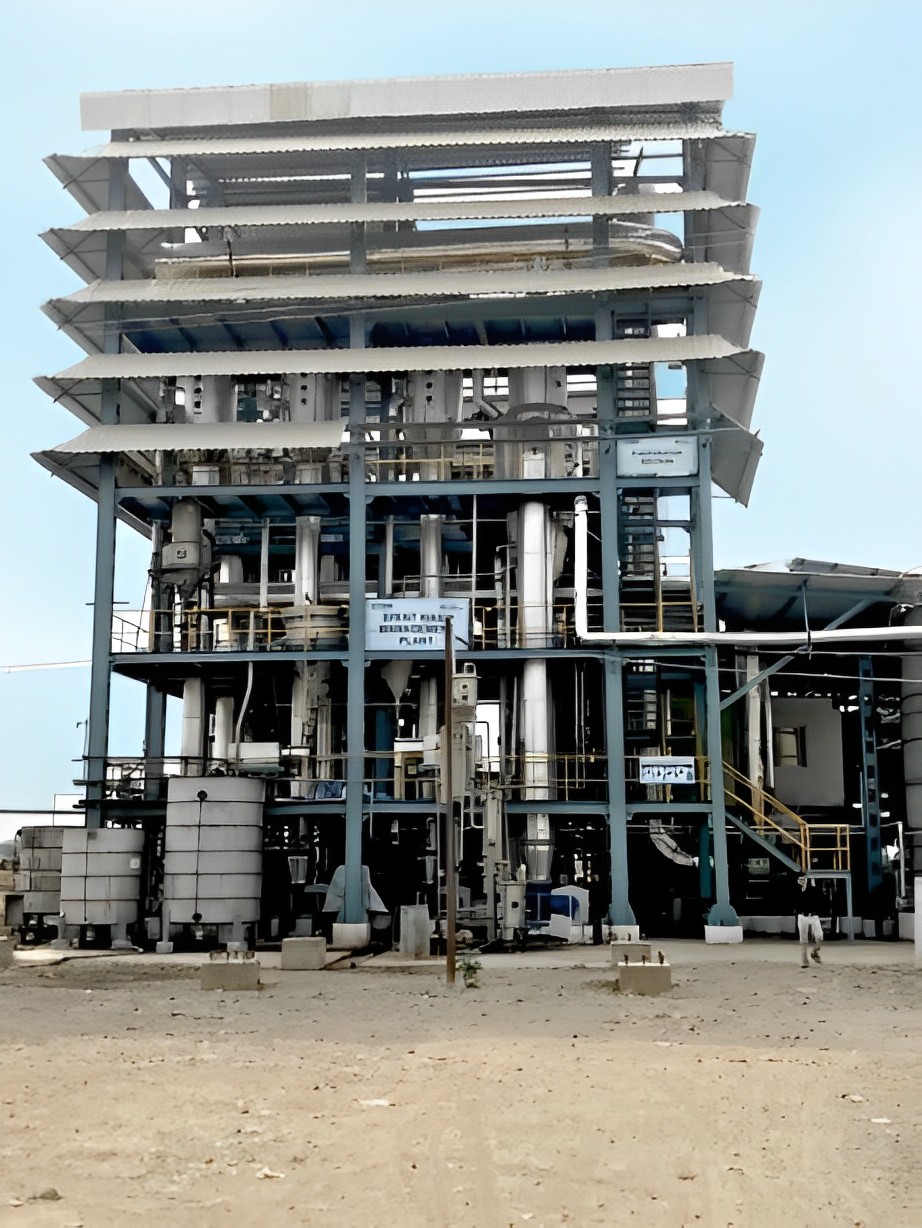
The Patented and innovative process can be easily installed in any Distillery. The Spent-wash produced in the distillery is the main waste stream that needs to be treated as the same is termed a pollutant. Our technology is based on Thermo-mechanical Reaction and Crystallization method.
POTASH (K2SO4): With the use of Advanced Salt Separation Technologies, clubbed with using basic raw materials, Catalysts for Thermo-Chemical process the Extraction of Potash is done organically and in the purest form. This Potash is extracted in the form of widely used SOP (Sulfate of Potash) or K2SO4
CMS or DPV: During the process, the Concentrated Spent is de-potash (CMS or DPV), and the same has been approved by NDRI – Karnal Cattle Feed division and NDDB Calf Division for the use as an alternative cattle feed binder. The Department of Animal Husbandry also has acknowledged the use of the same as a Cattle Feed Binder.
Water will be recovered from Evaporation Unit and Crystallizer Unit which will be sent to the existing CPU. However, during the process there will not be any acidity left which can reflect in Condensate and hence neutralization is not required. Hence TDS in the Condensate will be very less (possibly less than 500 ppm).
Process Benefits
Evaporation is a pure separation method and offers the most efficient ways to recover valuable salts. Since this method just gives physical separation, the chemical properties of the components separated do not change. Different pre and after treatment technologies like RO, Membrane Bi-reactor, Activated Carbon Filters, Peroxide Oxidation etc. are available, which always help in generating extra purity of the compound separated We strive to bring the best technologies for energy efficient and pollution free environment.
Energy Efficient Design
The system is directly heated, hence a fair amount of energy can be recovered by using evaporated water for other process or for heating purposes. Multi-stage designing can help utilize the heated vapor of one stage to other stages, hence lowering down the steam consumption. Utilizing evaporate vapors of first stage of Evaporator through Mechanical Vapor Recompression (MVR) or Thermal Vapor Recompression (TVR)
Advantages Of Our Method Of Treatment
- Recovery of FCO Grade Fertilizer Grade ‘Potash’ for use in Fertilizer (Value addition), completely soluble in water
- Reduction of Spent Wash volume Evaporation plants, increasing the efficiency, with a reduction in Steam and Power consumption.
- Desalted and organic Free CMS for:
- Nutritious Additives for Cattle Feed
- Steam & Power Generation by non-conventional means
- Efficient Gasification
- Recovery of Water for Process Reuse and Recycling
- Reduction in POTASH import,
- Perfect Import Substitute for SOP (Sulfate of Potash) and MOP
- Practically and scientifically achieving Zero Liquid Discharge
- Supporting the Ethanol Policy of the Government of India, which will make use of CMS as Cattle Feed Molasses alternate, hence providing additional molasses for Alcohol Generation
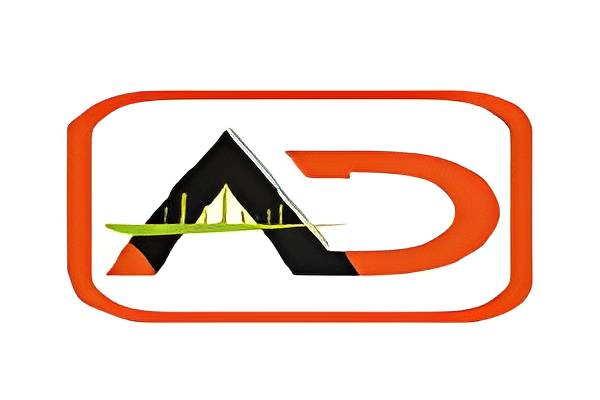
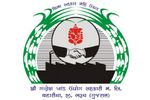

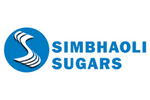
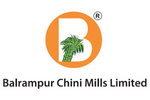
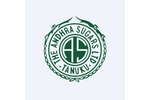
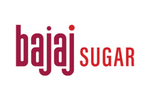
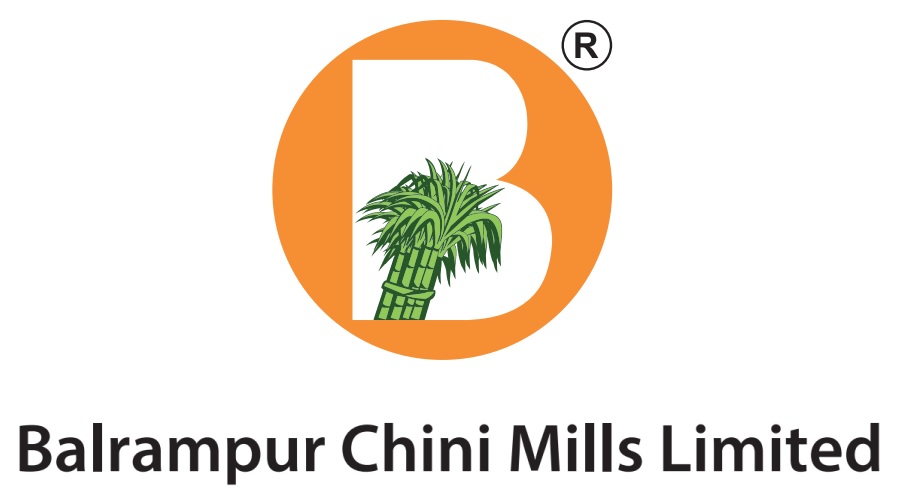
