Dryers
"Robust Design, High Thermal Efficiency, Selection based on Application"
Agitated Thin Film Dryers (ATFD)
Due to its inherent design features, it is ideal for thermal treatment of solutions and heat sensitive products, where reduced operating temperatures and vacuum operating pressures are desirable. The typical Agitated Thin Film Evaporator consists of a tubular heat transfer area with an external heating jacket and a fast-revolving, inner rotor with flexible or rigid wiper elements. The driving speed is adapted to the product being handled, its particular specifications and task.
The feed product is evenly distributed by the rotor and its wipers over the heating surface, forming a thin liquid film of uniform thickness. Highly turbulent swirls are produced at the tip of the rotor blades and wipers with intensive mixing and agitation of the product, as it comes into contact with the heating surface. This assures excellent heat transfer combined with constant renewal of the product film and provides an even heating and short residence time of the product through the heated zone.
Key Advantages
- Good heat conductivity (k-value), even when working with highly viscous and contaminated products
- Minimal thermal stress, thanks to low operating capacity, therefore a short dwell time (10-20 seconds of mean dwell time)
- No dead zone, therefore overheating prevented and perpetual high product quality guaranteed
- Continuous mechanical cleaning of the heating surface prevents incrustations
- High evaporation rates, due to highly turbulent film and large difference in temperature
- Gentle evaporation, due to short residence times, rapid conveyance in the heated zone and the constant product film renewal, happens often
- Combined with suppressed boiling points due to operation under vacuum
- Reduced need for maintenance because of sophisticated bearings and shaft sealing parts
- Shorter downtime and assembly time for maintenance and inspection
- No corrosion as outside surface is usually made of stainless steel
- Evaporation in one pass, no circulation
- Small film thickness, no hydrostatic height
- High turndown ratio and high flexibility for variation in requirements
- Low operating pressure down to 1 micron to reduced boiling temperature
Applications
Mainly used for difficult vaporization and heat exchange processes, especially where products to be handled are highly viscous and conventional plants can no longer meet user demands because heat transfer is insufficient. Due to the liquid film, mechanically generated on the heating surfaces, thin film equipment achieve much better heat transfer rates, even with highly viscous products containing solids.
- To concentrate highly viscous products, polluted liquids, salt solutions, oils, resins, etc
- As a sump evaporator for vacuum rectification columns
- Sludge drainage
- To continuously dry powdery residues
- Distillation of high-boiling substances under high vacuum
- Degassing and/or removal of volatile components of highly viscous products
- Heating or cooling of viscous solutions
- Improve product quality by removing colour bodies, minimizing impurities and eliminating thermal degradation
- Increase product recovery by reclaiming additional bottoms product from overhead and distillate products from bottoms
- Separation of close-boiling compounds
- Enhance product recovery
- Recovers additional bottoms product from overhead
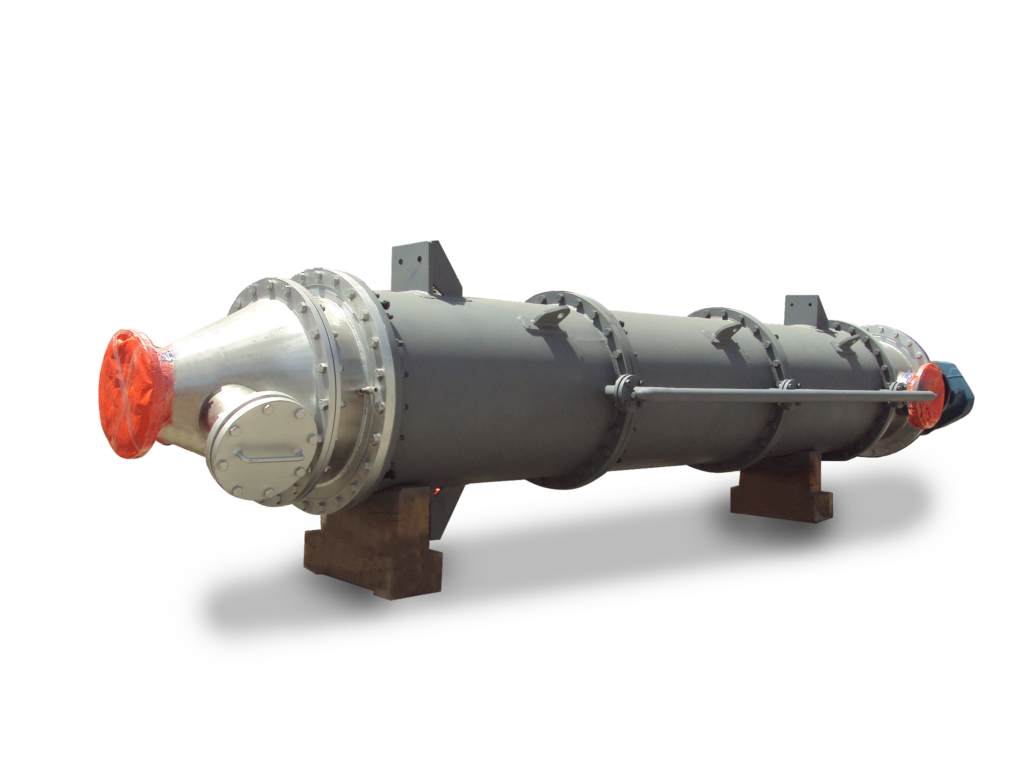
Agitated Nutsche Filter Dryer (ANFD)
Nutsche Filter is a mechanically agitated dryer. It is multi-utility equipment, combination of filter and dryer, thus reducing number of equipments in downstream, energy consumption, labour thus improving profitability. It is a closed vessel designed to separate solid and liquid by filtration under pressure or vacuum. The closed operation ensures odorless, contamination free and nonpolluting working conditions maintaining product purity and hygiene. The advanced technology of agitation and hydraulics used in the equipment makes it versatile and user friendly. The resulting wet cake can be slurrying and washed thoroughly with water or solvents unlike in centrifuges.
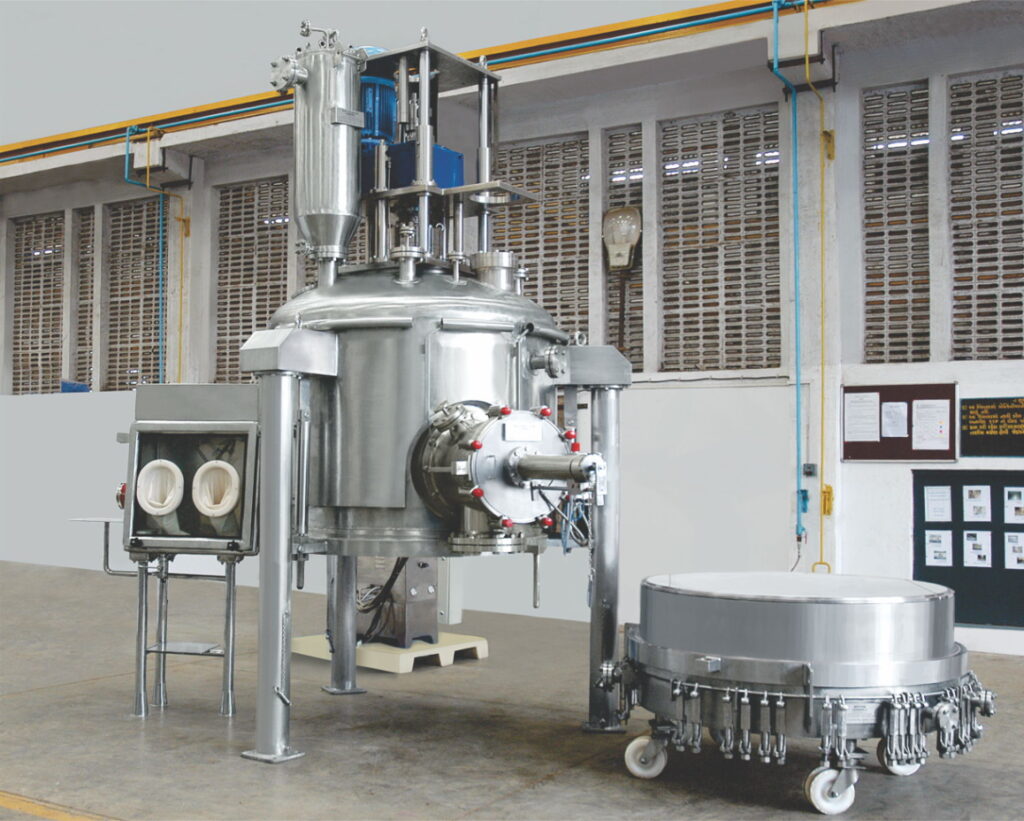
It is constructed with a top dish end and a flat bottom. Feed usually enters from the top, while the bottom end is welded with supports as it houses perforated plate. Drying of wet cake is also possible when heating is provided on shell by limpet.
Construction :
It is suitable for filtration of liquids with a high solid content. It is totally enclosed and is normally operated under pressure or under vacuum. Additionally, the equipment is fitted with a stirrer mechanism which efficiently agitates the slurry during cake washing, smoothens and squeezes the cake during filtration and assists in the automatic discharge of the cake. A main shaft rotates and also moves in the vertical direction. Specially designed ‘S’ shaped stirrer blades are mounted on the shaft, capable of performing various function such as cake smoothening, vigorous agitation and cake discharge. A side discharge arrangement is provided, closing and opening through hydraulic / mechanical means. A filter plate is located at the base of the vessel in level with the discharge port. Bottom plate is provided with stiffeners in order to provide support for filters to facilitate flow of filtrate. Suitable nozzles, man hole and side discharge provided as well. Hydraulic/Mechanical means are provided to facilitate opening of side discharge.
Paddle Dryer
Chem Process Systems manufactures paddle dryer, which is conduction type dryer, aiming towards Zero Liquid Discharge (ZLD).
It’s an energy saving, vapor-sealed dryer which has the capability to handle both organic and in-organic granular & powder materials.
Working :
- Paddle dryer operates by indirect heating or cooling of the product. The product is brought into direct contact with revolving, cuneiform shaped hollow heaters, using conduction as mode of heat transfer.
- Rotating paddles function as heater in this type of dryer. Because of this feature, a paddle dryer is able to provide large heating surface area with compact design.
- As paddles are the only major moving component, it offers variety of advantages:
- High thermal efficiency
- Compact equipment- reduced floor space
- Low air requirement
- Uniform and controlled drying
- Wedge shape design of paddles offers heating on both surfaces as well as self-cleaning action
- Residence time for the product can be controlled
- Minimal maintenance and easy accessibility
- Precise control of temperature
- Can handle hazardous materials
- Inert process during operation
- Robust
- Uniform product quality
- Arrangement is kept in an inclined fashion and feed is provided from unloading end. Because of this arrangement the work of transportation of the product from end to end is done by gravity. The paddles then just work on drying and mixing of the product.
- Heating medium can be oil, water or steam
Paddle dryer can handle sticky, pasty materials without the need of prior conditioning. Thus resulting in lower capital requirement.
Indirect heating has some notable advantages over direct heating:
- Product never interacts with heating medium directly
- Little or no dust formation
- Recovery of solvents is simple
- No need to separate heating medium from product
- Toxic, odorous and flammable products can be processed safely
- Chemical integrity of the product is maintained
Sludge management is an ever increasing problem due to environmental pollution and energy consumption. Sludge production is estimated to double within a decade and drying is now widely recognized as an efficient means of processing different kinds of sludge. Following are the main application of paddle dryer:
- Industrial Applications
- Chemicals
- Pharmaceutical
- Food industry
- Process Based
- Drying
- Heating
- Cooling
- Roasting
- Melting
- Cooking/Braising
- Calcinations
- Sterilization
- Crystallisation
- Removal of solvents
- Steel and Mining
- Pyrite copper concentrate
- Coal
- Aluminum Hydroxide
- Manganese Dioxide
- Waste Water Treatment
- ETP sludge
- Biological sludge
- Municipal sewage sludge
- Sludge from textiles
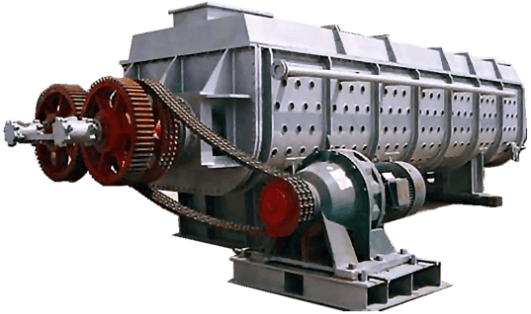
Flash Dryer
Flash Dryers have the unique benefit to evaporate moisture rapidly with a very low residence time.
These sort of Dryers are generally utilized for applications involving Wet Cakes, Powders, Granules, Lumps products. In these dryers, the feed is dispersed in a stream of hot air at significant velocities and are dried.
Flash dryers are custom designed to suit varying residence times based on the end product requirement.

Special feed conditioning equipment are integral to this dryer to take care of uneven feed cake moistures. Feed cake moisture contents from 5% w/w up to 87 % w/w can be handled in these dryers. Chem Process Systems Flash Dryers are custom designed for feed capacities ranging from 50 kg to 10000 kg / hr.
Applications
- Pigments
- Optical Brightening Agents(OBA)
- Intermediates
- DASA
- 6- Acetyl OPASA
- H-Acid
- OAVS
- Para Phenylenediamine
- Vinyl Sulphone
- Sodium Sulphate
- Di Calcium Phosphate
- 2-4 D Sodium
- Glyphosate
- Acephate
- Starch
- Gluten
- Fibre
- Dextrose Monohydrate
- Dextrose Anhydrous
- Metallic Stearates
- Zinc Borate
Cage Mill Flash Dryer
When the feed cake is very hard or has a tendency to lump or crust while drying and needs to be simultaneously disintegrated and dried then dryers with Cage Mill disintegrators are used. The advantage of this Dryer is to handle the Hard Cakes, Crusts, and Lumps
In this Type of Dryer, Both the Feed and the Hot Air enter the Cage Mill Dryer simultaneously into the ‘Eye ‘ of the Cage Mill Disintegrator.
The Cage Mill design consists of an Vertical Mounted Rotor enclosed in Casing having Stator Plates. This dryer is also commonly called an Attritor Mill type Dryer.
Cage Mill Flash Dryers are custom designed to suit feed capacities ranging from 100 Kgs / hr to 3000 Kgs / hr.
Applications
- Intermediates
- DASA
- 6- Acetyl OPASA
- H-Acid
- OAVS
- Zinc Borate
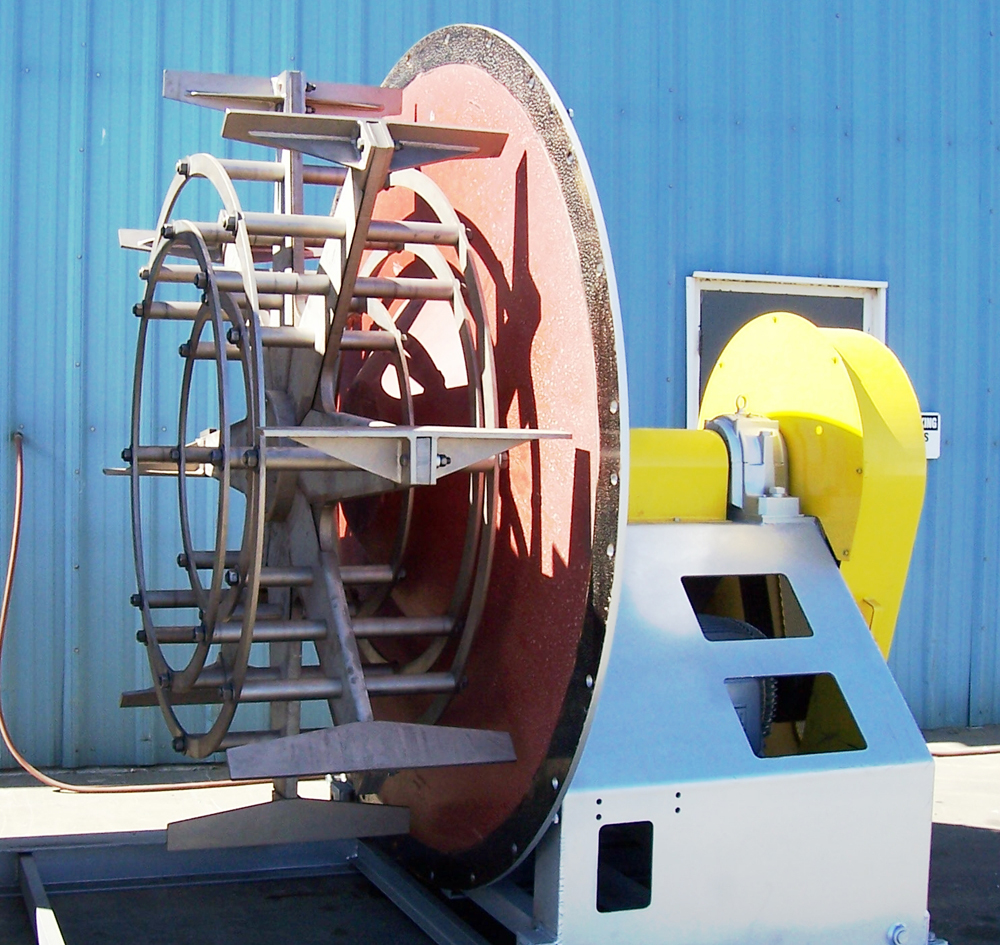
Spin Flash Dryer
Swirl Agitated Flash Dryers are ideal for Drying Sticky, Thixotropic Cakes. In these Dryers the wet feed in introduced in a Swirling Fluid Bed of Material. The Bed is kept in continuous Agitation by means of an Agitator mounted at the bottom. The adequate residence time of Drying is provided in the Dryer. The particle size of the final product can be controlled in this Dryer.
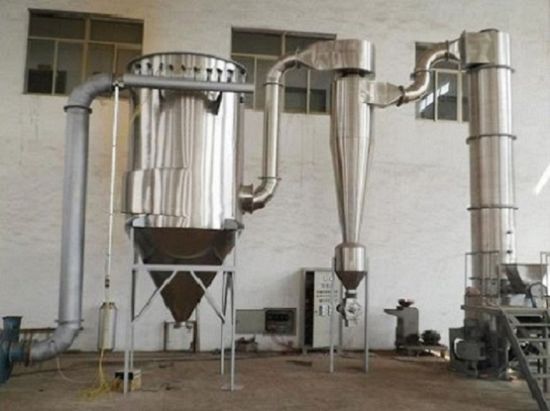
If the Cake is Solvent Laden, then closed loop designs of the Swirl Agitated Dryer operating with Nitrogen as the Heating Media are available.
CHEM PROCESS offers Swirl Agitated (Spin)Flash Dryers with feed capacities ranging from 50 Kgs/hr to 6000 Kgs/hr
Applications
- Pigments
- Optical Brightening Agents(OBA)
- Intermediates
- DASA
- 6- Acetyl OPASA
- H-Acid
- OAVS
- Sodium Sulphate
- Di Calcium Phosphate
- 2-4 D Sodium
- Glyphosate
- Acephate
- Gluten
- Fibre
- Metallic Stearates
- Sludge
Drum Dryers
The simplest and least expensive is the drum, or roller, dryer. It consists of two large steel cylinders that turn toward each other and are heated from the inside by steam. The concentrated product is applied to the hot drum in a thin sheet that dries during less than one revolution and is scraped from the drum by a steel blade. The flake like powder dissolves poorly in water but is often preferred in certain bakery products. Drum dryers are also used to manufacture animal feed where texture, flavor, and solubility are not a major consideration.
Drum dryers are of conductive heat-transfer type. A heating medium (generally steam) is sent into the rotating drum (cylinder) and liquid material is fed on the heated drum to evaporate and concentrate, and concurrently the liquid material is stuck on the drum surface in the form of a film, then promptly evaporated and dried. Dried materials are scraped continuously with a stationary knife.
Drum dryers are roughly classified into an atmospheric type and vacuum type according to operating pressures, and also, they are classified into a double drum type, twin drum type, and single drum type according to the number of drums.
Further, the single drum type is classified into a dip type, spray type, splash type, top roll type (single-stage, multi-stage), side roll type, below roll type, etc. according to the liquid feeding methods. These classifications are based on the trial for making materials adhere to the drum surface more uniformly and efficiently. Scraper knife no pressing type and drum material of carbon steel with clad steel are available in accordance with its application. These Dryers are generally available in a operating range of 25kg/hr to 2500 kg/hr capacity
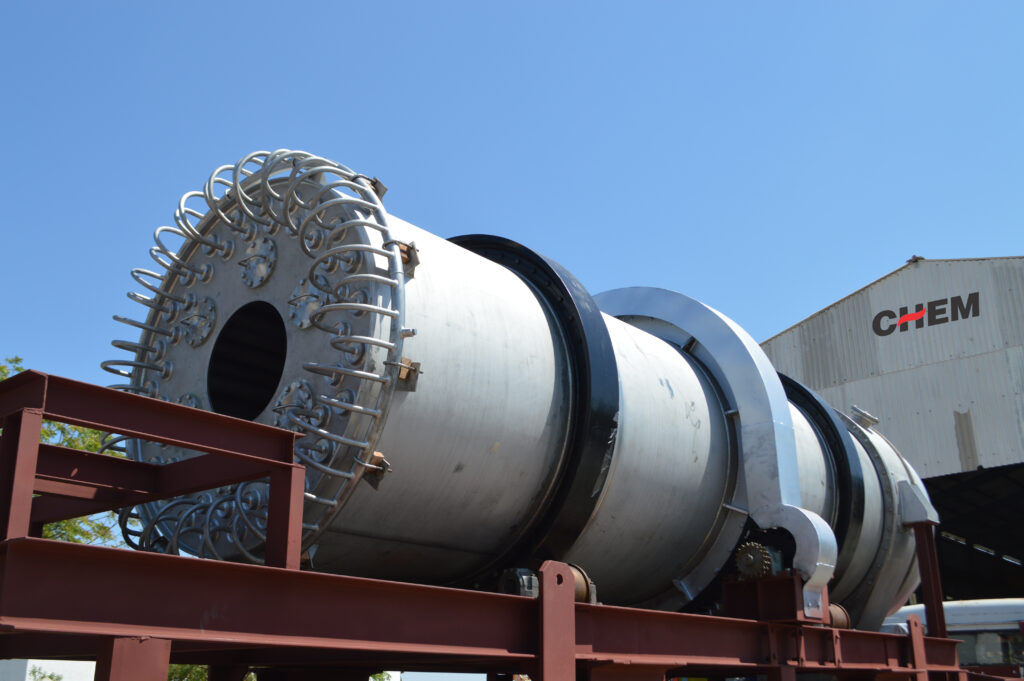
Batch Dryer
Batch Type Dryers uses a perforated belt to transfer feed materials through the dryer. Heated air is either passed under and through, or over and through the belt and product bed before being reheated and re-circulated. Units are normally multi zoned and may have differing airflow's in successive zones. Additionally each zone may use a different temperature profile and control. Saturated or close to saturated air is exhausted from the dryer via a central exhaust duct.
Batch Type Dryers may be multi pass units, in which the feed is transferred from one belt to another belt below it by gravity. These dryers are usually two or three pass machines. Additionally certain conveyor dryers, such as those used in vegetable dehydration have multiple belts in line, and the feed is transferred from one belt to another.
Feeding / discharge Manual, batch, automatic and continuous. Vibrators, oscillating feeders, gravity chutes Feed Characteristics Large granules, agglomerates, pellets, preformed (extruded) products (pressure agglomerates), small solid particles, large solid particles, agricultural products. Low to high feed rates

Heat Source Steam, electrical, coal, liquid fuels, or gas Exposure Mostly Direct. Flow can be through the bed (under to over, over to under, or both), cross, counter current or co-current. Indirect systems available for certain products. Residence time Highly Controllable. Residence time can be altered by varying the feed and discharge rates affecting the bed depth. Belt can be slowed and modulated.
Extraction Normally central induced. Re-circulating fans used in each zone.
Exhaust connected to common header
Dust Collection
Typically little required. For fine product a central bag house is sometimes used
Benefits
- Very intimate contact with air/gas stream
- Good for heat sensitive products and products requiring long residence times
- Energy efficient due to recycling of process air Multiple zones offer flexibility for temperature and process control
- Excellent transfer of energy
- Can vary flows between zones
- Gentle handling of product
- Self contained with distributed foundation loading
- Unit can have integral cooling section.
Limitations
- High temperature units can be troublesome
- Heater can clog on carryover
- Belt tracking can be problematic
- Belt may clog, requires frequent cleaning
- Loss of fimes through perforations on flights or belt
Conveyer Dryers
Conveyer Dryers are effectively used in many of the processes where a gradual and procedural drying is anticipated. Belt dryers in air recirculation mode for the continuous desiccation of bulk material have been the first choice. The air flow acting on the large surface of many individual particles is energy efficient and moisture absorbing and the moisture within the bulk only has to pass short distances.
The product is distributed on an endless, air permeable conveyer belt and is flooded with heated air. The drying air is circulated and saturated with each pass though the product layer. A specific part of the drying air is replenished with fresh air and at the same time corresponding vapours are removed. For optimum energy efficiency the drying air is directed against the product flow.
In case a uniform treatment over the entire product layer height required, the air direction changes at least once from upstream to downstream. Often a cooling section follows. Here, the cold air passes from top to bottom through the product. The heated exhaust air can be used for the drying section. In case of very slow running processes, our belt dryers can be designed as multi-belt systems.



