MVR type Evaporation Systems
"Chem Process designs, installs, and commissions Mechanical Vapor Recompression (MVR) technology-based Evaporator systems."
Mechanical Vapor Recompression
This mechanical compressor is most commonly driven with an electric motor. Utilization of the mechanical compressor substantially reduces steam requirements as well as cooling water demand. To keep the evaporation plant as simple as possible and for easy operation, single-effect centrifugal recompressors are frequently used. This can be highpressure fans or centrifugal-compressors. For high pressure increases, multiplestage compressors can be used. Evaporation plants equipped with mechanical-vapor-recompression-type heat pumps require low energy input during normal operation. Jet compressors can compress only a part of the vapor and the energy of the motive steam is discharged as residual heat via the cooling water. In mechanical vapor recompression systems, however, all vapors are compressed to a higher condensation pressure, as shown in the heat diagram. Some additional steam or condensation may be required to maintain the evaporator heat balance and give stable operating conditions. For lower evaporation rates, positive-displacement-type compressors such as sliding vane rotary compressors, or screw-type compressors can be used as well. This is rather rare, however. The specific energy consumption corresponds to the compressor energy input/evaporation rate ratio. This is determined by the compression ratio, which represents the temperature difference between the heating steam and boiling liquid. Furthermore, it depends on the boiling point elevation and the pressure loss in the system. Under favourable conditions this value can be as low as 4 kwh per 450 kgs. of water. Electric motors can be used to supply the motive power for the compressor. They are reasonable priced and easy to operate and maintain. Combustion engines have been used in cases where there is heat available from the cooling water and exhaust gas. If high-pressure steam is available, it is reasonable to install a steam turbine. Utilizing the turbine exhaust steam may provide very high total energy efficiency. With an MVR evaporator system efficiencies can run as high as 90 kgs. of water evaporated per kwh (roughly the equivalent of 25 kgs. water evaporated per kg of steam with a TVR evaporator). Chem MVR Evaporator Systems can be designed for rates from under 5 m3/hr to over 100 m3/hr. Mechanical vapour compressors contribute to lowering the power consumption during the Evaporation Process. The high quality fans used, are custom designed to suit to the needs of the Evaporation Plant, with the tremendous design experience that Chem has in-house.
Selection Criteria
Since prices for steam and electricity vary by region, the choice between MVR and TVR (and in the case of TVR, the number of stages) depends on local prices, possible utilization of hot condensate, and depreciation of the capital cost. Both systems produce the same product quality as long as certain critical design parameter requirements are met.
Characteristics
Vacuum-proof housing design, up to 0.1 bar (abs.). Rotors for extremely high circumferential speeds for increasing the efficiencies. Water jets for cleaning the rotors and for temperature re-cooling during operation. Low-wear labyrinth seals. Optional connection in series or parallel possible for larger pressure differences or volumetric flows. Compression oil vaporisation both for rolling bearings as well as for plain friction bearings enable design speeds well above the critical bearing speed and low vibration operation even during speed adjustment. Chem uses a new type of fan to series production stage, the rapid rotor MXDA, for smaller mass flow rates, primarily in wastewater treatment evaporators. Driven by a motor this machine runs with a speed of over 14,000 U/min. Thus, it is possible to use a centrifugal fan, even for small mass flow rates, to achieve temperature increases of up to 6.0 °C.
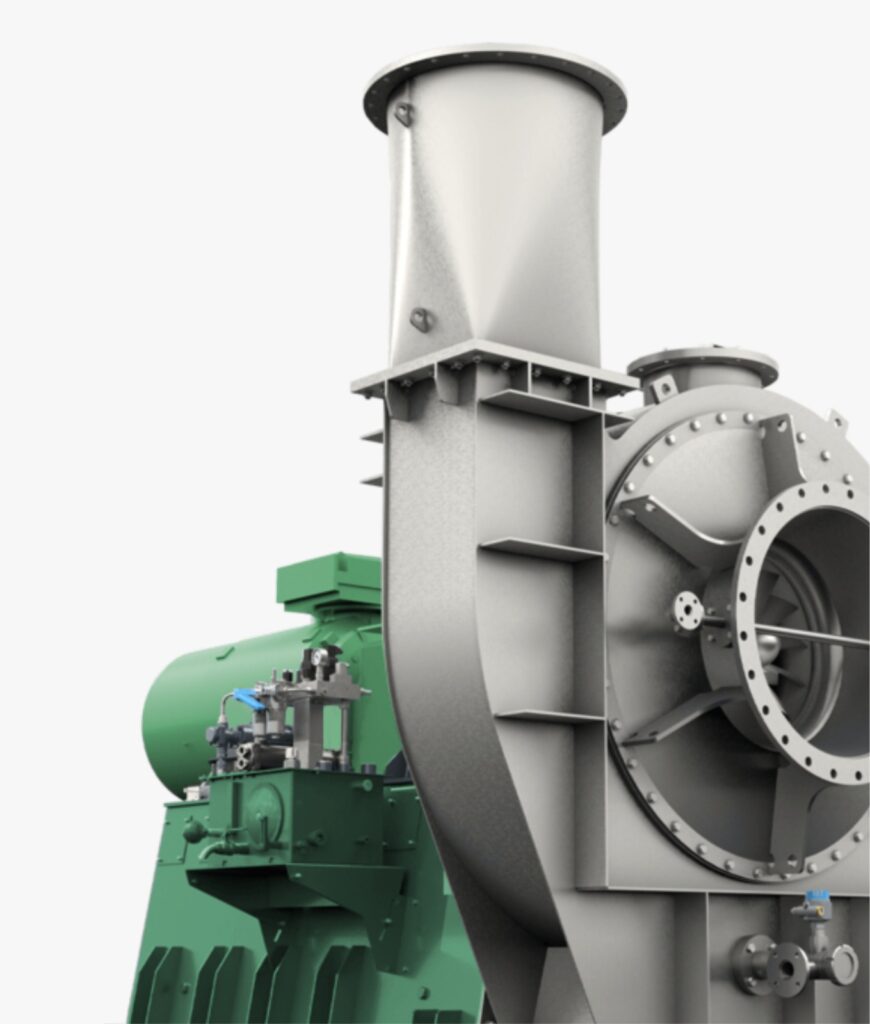
Applications
- Milk, whey and other milk products
- Sugar solutions
- Salt solutions,
- Sulphite liquors and in the chemical industry for,
- Vapourization crystallization of sodium sulphate
- Concentration of thiocarbomide solution
- Rectification of propylene
- Treatment of aqueous process liquids and waste waters by evaporation
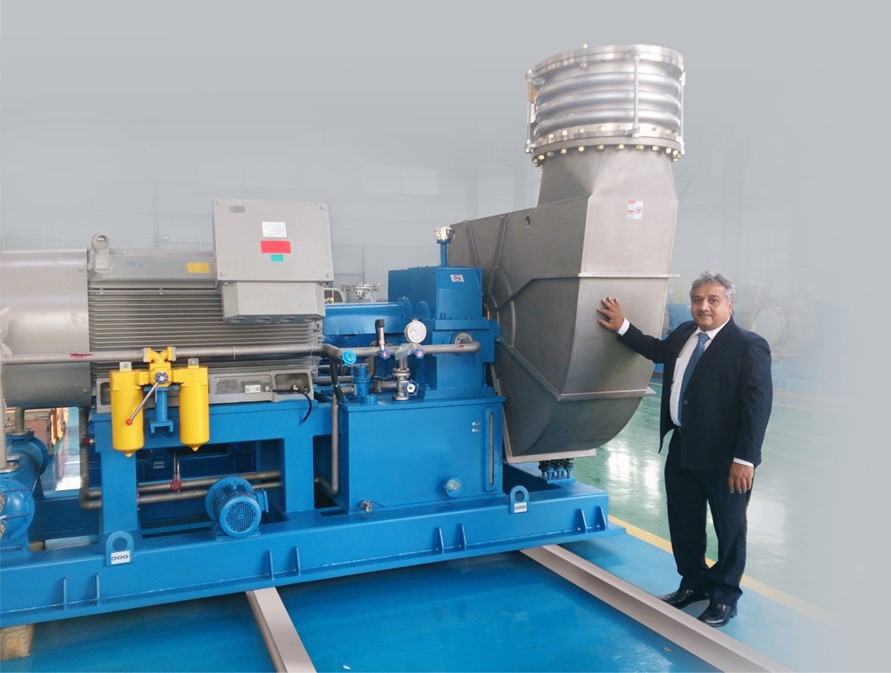
Operational Schematic Of System
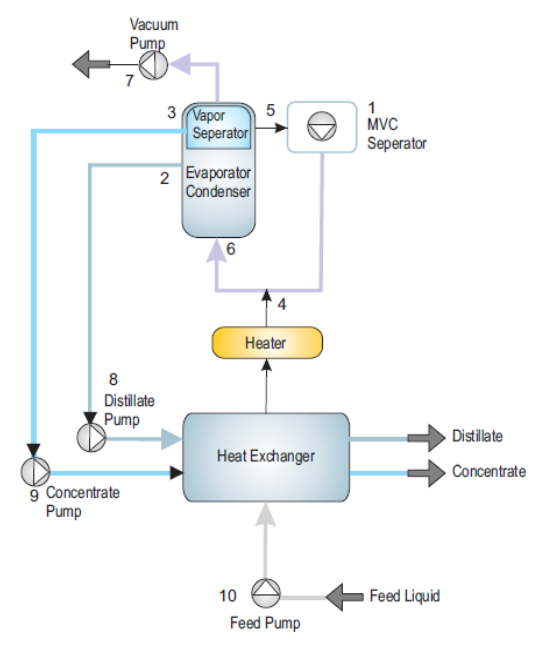
Operation Description
Entering impure feed liquid is preheated as it passes through a heat exchanger, which cools and recovers heat from the two exiting liquid streams- pure distilled water (2) and concentrated residues (3). Heated to within a few of boiling temperaure, the feed liquid next passes through a start-up heater, thent at (1) enters and evaporator/condenser comprising a bank of dynamic film metal thermal membranes. The feed liquid boils as it passes through the evaporator, and the steam vapor is drawn off at (5) by a centrifugal vapor compressor. The remaining concentrated liquid flows out at (3), carrying away all contaminants. The pure steam extracted by the vapor compressor, is pressurized - raising its temperature - and injected into the condenser at (6), where its latent heat is released through the dynamic thermal membranes at it condenses into pure distilled water, thereby causing the feed liquid to boil. Pressure differentials ensure the process is fail-safe. Because most of the process heat is recovered and recycled within the heat exchanger and the evaporator/condenser, overall specific energy requirements are dramatically educed in comparison with conventional distillation systems. In fact, following the star-up period, there is little or no energy required to directly heat the water. The only energy input needed to operate the system is used by the vapor compressor, four pumps (7, 8, 9, 10) and the controls. Evaporators can operate under a partial vacuum at (4), reducing the boiling temperature. Low temperature boiling reduces scale formation and heat exchanger fouling, minimizing maintenance, downtime and costly pre-treatment process. The boiling temperature remains high enough to kill and micro organisms except heat resistant spores, thereby rendering not only the pure distilled water but also the concentrated liquid stream that the feed liquid by inactivating all harmful biological organisms.
Advantages of Mechanical Vapour Recompression Evaporator with Turbo Fan /Compressors
- Most energy efficient.
- Various system concepts, one or two stages
- Atmospheric or vacuum operation
- Low retention time, optimum quality
- CIP system according to client need
- Flexible arrangement of body and fans
- None or minimum cooling water required
- Computer based operation and control
- Ideal for heat recovery from condensate
Heat Diagram
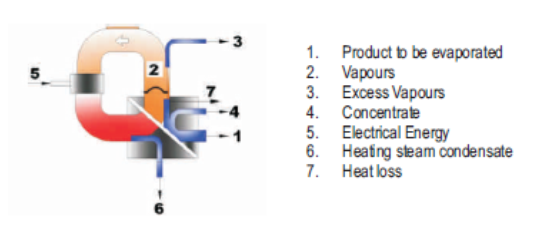
Features
External straight tube preheaters give short residence time, better
- Deaeration of the calandrias, and easy inspection and cleaning.
- Static liquid distribution system ensures that all tubes in the calandrias
receive equal amounts of liquid at all times and can accept wide variations in
liquid flow and flash vapor. - Chem’s freestanding design reduces floor space requirements and building
costs, and is flexible in arrangement for installation in existing buildings. - Efficient liquid-vapour separation result from controlled vapor vellocities with
tangential inletand outlet ensuring minimum pressure losses. - Cleaning costs are minimized by CIP producers, which may be fully automated.
- Instrumentation is per customer requirements, inlcluding PLC controllers that
can optimize product and quality.
Process
The evaporated vapour passes through a compressor or high pressure fan where the pressure of the vapour is increased by a factor of 1.2 to 2.0. The increased pressure of the vapour enables it to provide the energy and temperature difference required for evaporation. Evaporation by means of mechanical recompression can be more cost effective than TVR evaporation. The MVR design used for pre- concentration (before entering an evaporator for high solids concentration) in place of a membrane system is highly efficient and requires very little maintenance. The high efficiency of a Chem MVR Evaporator System can make an important contribution to your energy savings program.
MVR evaporators with fans are prevalent within the food industry. The MVR evaporator is often applied as a pre concentrator followed by a finisher. MVR's are predominantly used in the food industry for the evaporation of,
Applications
- Milk, whey and other milk products
- Sugar solutions
- Salt solutions,
- Sulphite liquors and in the chemical industry for,
- Vapourization crystallization of sodium sulphate
- Concentration of thiocarbomide solution
- Rectification of propylene
- Treatment of aqueous process liquids and waste waters by evaporation
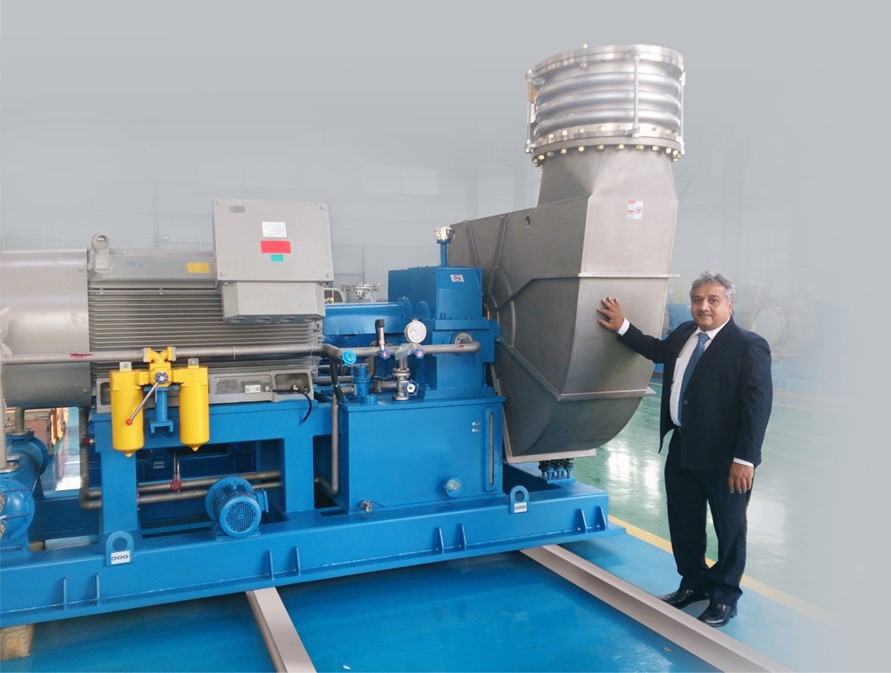