Gas extraction and Generation
"Process Designed for Fine Crystal Growth and Salt Recovery"
PSA Systems
- Oxygen Recovery Plants – from 15 Nm3/hr
- to 100Nm3/hr
- Nitrogen Recovery Plants
- Methane Cleansing Units
- Biogas produced from various feedstock
- contain Methane, Carbon Dioxide, Hydrogen
- Sulfide and other impurities with moisture. Bio-gas application requires purity of methane with
- minimum impurities. Chem Process has
- developed Cost Effective and Reliable Bio-gas Cleaning Systems producing Bio-CNG with 96%
- Methane, Maximum 3% CO2, less than 20 PPM
- H2S and less than 100 PPM Moisture
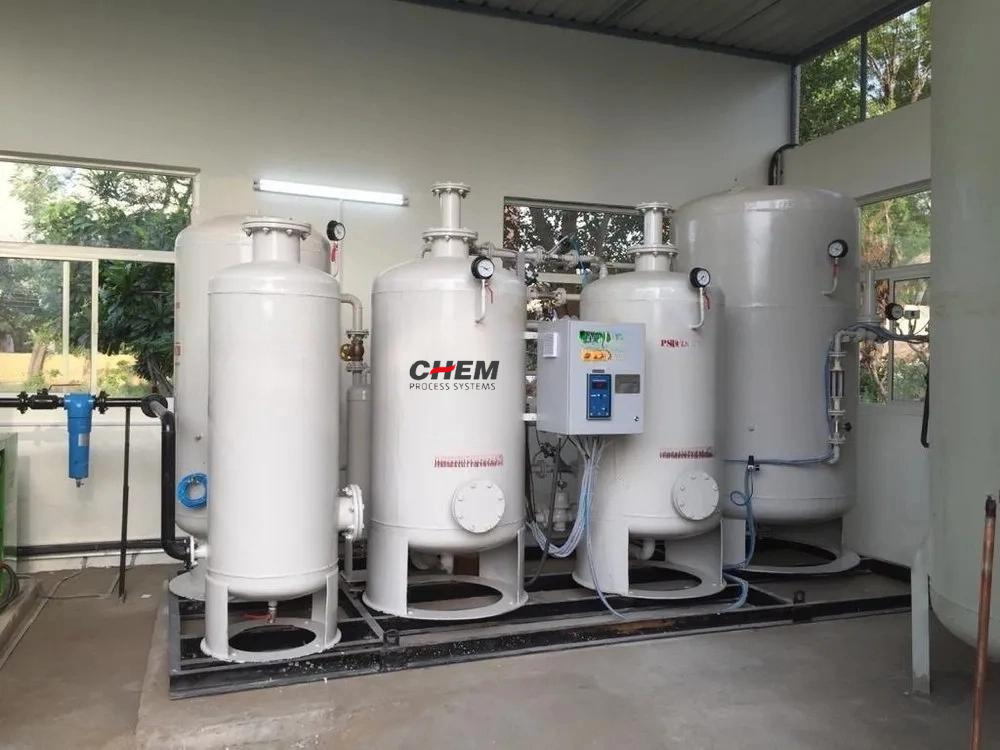
PSA Oxygen Generation plant
Our Oxygen Gas Plant work with PSA (Pressure Swing Adsorption) technology. Using this technology, we produce oxygen gas plants that are highly economical and require low maintenance and produce the desired results in a hassle-free manner. These generators absorb nitrogen with the help of two absorption vessels that are filled with most efficient zeolite molecular sieves responsible for nitrogen absorption. In the Oxygen Gas Generation Process, the air is taken from an air compressor and oxygen is separated from other gases, including nitrogen with the help of zeolite molecular sieves. The process involves two towers filled with zeolite molecular sieves which adsorb nitrogen and subsequently discharge waste. The oxygen generated is 95% pure. When nitrogen saturates from one tower, this process changes over to the other tower, thus helping in the process of continuous oxygen generation.
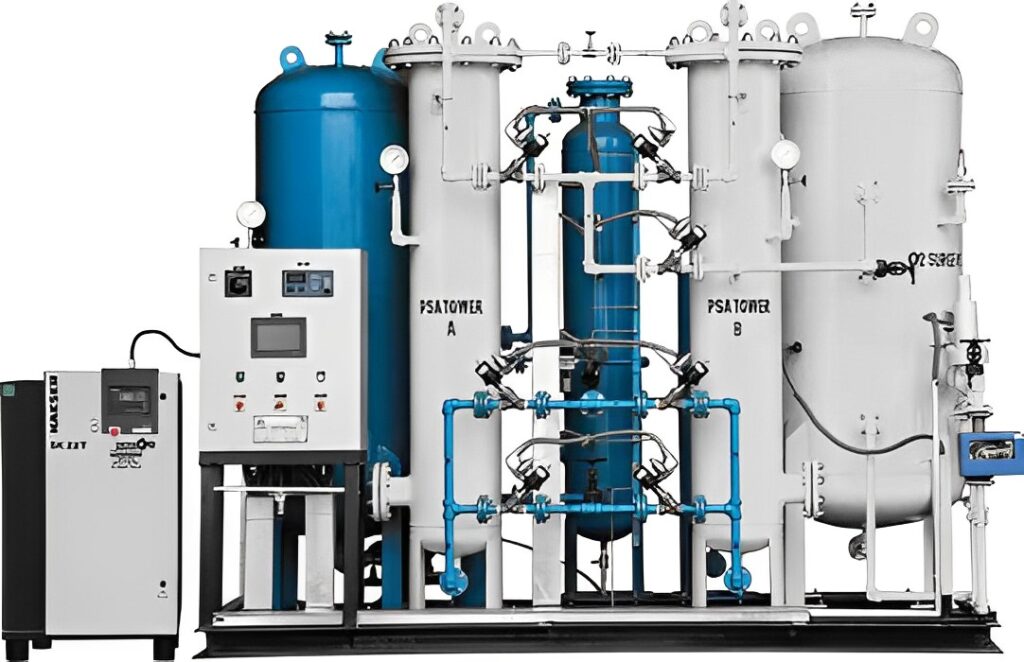
Salient Features
- Full Automation All systems are designed for unattended operation and automatic Oxygen demand adjustment.
- Lower Space Requirement The design and Instrumentation make the plant size very compact, assembly on skids, prefabricated, and supplied from the factory.
- The Fast Start-up time is only 5 minutes to get desired Oxygen purity. So these units can be switched ON & OFF as per Oxygen demand changes.
- High Reliability Very reliable for continuous and steady operation with constant Oxygen purity. Plant availability time is better than 99% always.
- High Reliability Expected Molecular sieves life is around 10 years i.e. whole lifetime of the Oxygen plant. So no replacement costs.
PSA Nitrogen Generation plant
Our Nitrogen Plant operating on PSA technology, consists of twin tower system filled with special grade of carbon molecular sieves (C.M.S.) at a time, one tower keeps in production cycle and other in regeneration cycle. When compressed air passed through C.M.S. bed, the molecules of oxygen, moisture & other unwanted gases are adsorbed on surface of C.M.S. and the nitrogen which is not adsorbed by C.M.S comes out of adsorption tower and is collected in a surge vessel.
PSA Nitrogen Gas Plant is provided, if the requirement at the discharge is at higher pressure. Normally our PSA system can provide pressure at discharge to about 6 kg/cm2g but it can be increase up to higher pressure of 150 kg/cm2g based on client's requirement. for this we need additional booster, suction pot and finned cooler after the surge vessel so as to enhanced the pressure up to higher pressure before storage tank.
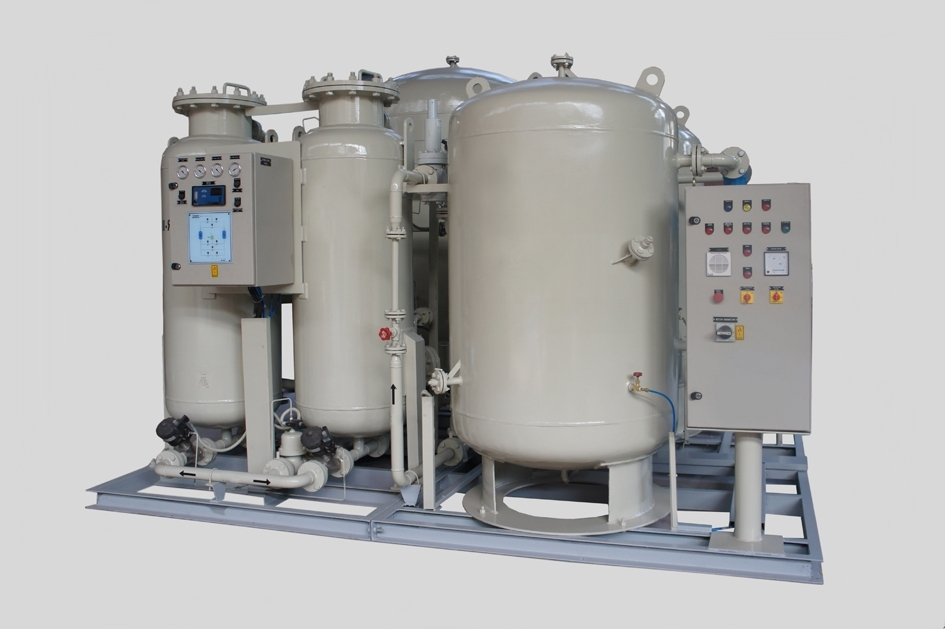
It is most economical to produce 98% pure N2 from PSA Plants. For applications which permit upto 0.5% Oxygen impurity, 99.5% pure N2 is generated by PSA Plants only. For Applications requiring better purity, 99% pure N2 is produced by PSA Plant followed by a Deox Catalytic Purification Unit, so that oxygen in the product nitrogen gas is brought down to level of 3 PPM.
Salient Features
- Instant on-site production of nitrogen of desired purity.
- Our equipment is built to meet the most stringent protective atmosphere requirements
- The unit is compact and mounted on skids.
- Low initial investment.
- Low operating cost.
- Utilities required are power and cooling water only.
- Fully automatic operation without any continuous supervision.
- Maintenance-free round-clock supply.
- Custom-built units to suit individual requirements.
- Well-proven design and technical backup support from the inventors of the technology.