Waste Water Treatment
Industrial produce of Waste water or commonly termed as effluent have different characteristics based upon the solid content, soluble content and oxygen demands as per the industrial segment.
Due to various norms the water has to be treated by means of different methods separating pure water from rest of the content.
Chem process has a unique range of processes to take care of your effluent starting from
- Forced Circulation Evaporation plant
- Rising Film Evaporation plant
- Falling Film evaporation plant
- Plate type Evaporation plant
- Crystallizing units
- Adiabatic type crystallizers
- Oslo Type Crystallizers
- Draft and Baffle Tube Type Crystallizers
- Induced circulation-type Crystallizers
- Natural circulation evaporation plant
- Combination of the above systems
- Stripping units
- Degasifiers
- Dryers
- Agitated thin film dryer
- Drum Dryer
- Paddle Dryer
- Screw Conveyor Dryer
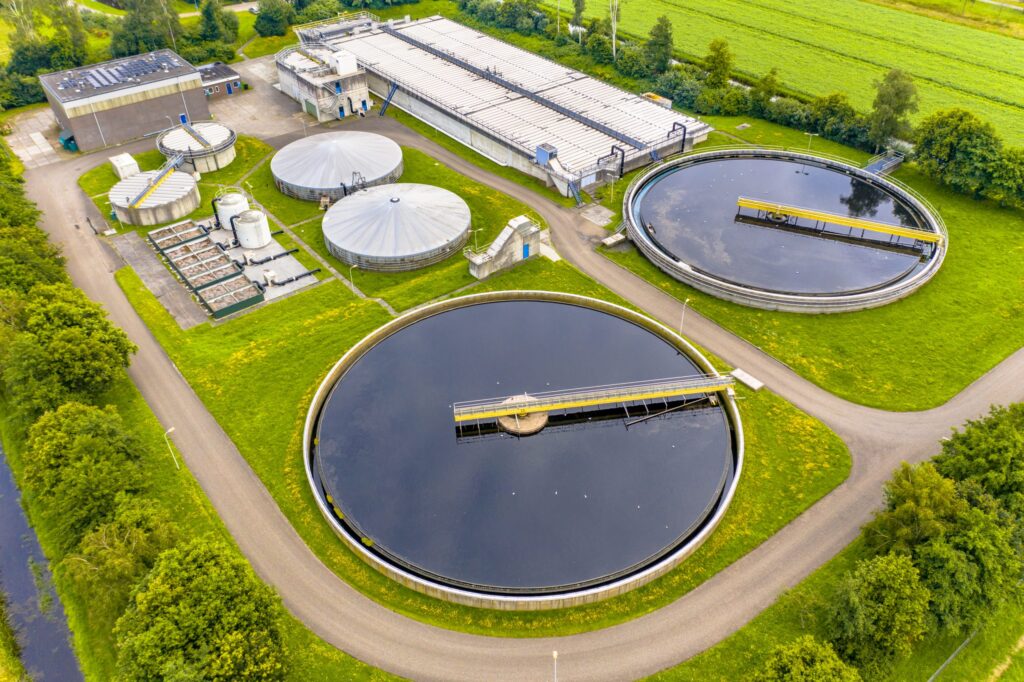
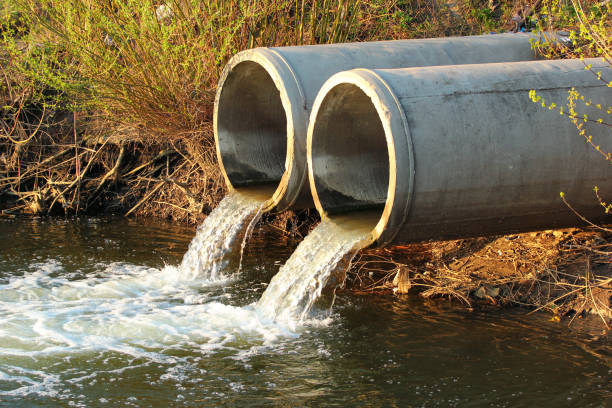
Treatment of Waste Waters from Chemical Productions/Processes
In the production processes of various pharmaceuticals, bulk drugs, agrochemicals, pesticides, dyes, dyes intermediates, textile, power, water treatment, galvanizing and various other chemical industries; waste waters produce essentially consist of several organic components, salts and water. Treating these waste waters is very difficult as they are toxic and cannot be treated in a bio-reactor due to high salt contents and hence also hinder dumping. The only method of disposal is to remove all the water, solvents and produce solids for reuse/disposal. In case of high COD contents having high boilers, the only option of disposal is by incineration. In such cases too, concentration prior to incineration is recommended. Both these tasks of concentration and separation can be optimally achieved with thermal treatments, technologies consisting of evaporation and crystallization.
Process Description :
The water portion is concentrated in the evaporation plant. The salt is separated by crystallization which may be by way of evaporative crystallization or a separate crystallizer arranged downstream of the evaporation plant. Then if required the volatiles are removed from the vapor condensate in a rectification column/stripping. Thus only the concentrated organic matter which is very small in quantity has to be incinerated.

Treatment of Waste Waters from Biotechnological Processes
Production / Processes :
In biotechnological production/processes, a biological treatment is not efficient, or is too complex because the continuation levels of organic substances and salts are very high. However these contents may be suitable for the production of fertilizers and animal feeds/fodder. Hence the best treatment solution for these waste waters is to first concentrate them in an evaporation plant and then dry the residual matters for further use in the production of fertilizers/animal feeds/fodder.
Biotechnological Processes :
- Drinking Alcohol Production
- Ethanol Production
- Glutamic Acid Production
- Lysine Production
- Yeast Production
Process Description :
Here usually the evaporation plant is of multiple effect and the configuration consists of a combination of falling film followed by forced circulation effects for concentration of the waste waters. Heating mediums and plant layouts are on the chemico-physical properties of the waste water and the available utilities. Waste energy from available sources and evaporator vapors can be utilized to optimally heat the evaporator. The condensate can most of the times be reused in the production process.
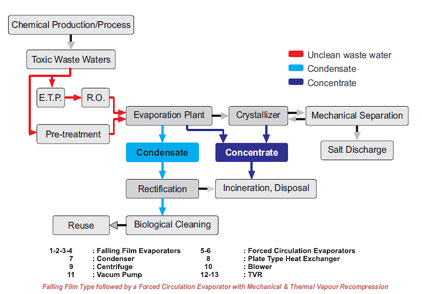
Treatment of Waste Waters of Food, Starch and Distilleries
Raw materials for bio-gas production are so-called fermentation substrates, such as corn, grain and grass, stillage from distilleries, manure, biological waste, remains of food and other fermenting residuals. After the anaerobic fermentation there are fermentation residuals, a mixture of persistent organic substances. The disposal of these fermentation residuals is decisive for the costefficiency of a bio-gas plant. Its storage and transport to agricultural areas is cost-intensive since the produced fermentation residuals are large (water contents 90 – 95 %).
Evaporation strongly reduces the quantity of fermentation residuals and therefore contributes to a solution of these problems to a large extent. The efficiency of evaporation will be particularly high if waste energy sources, such as vapor from a drying process or hot water from gas motor cooling can be used as heating medium.
Process Description :
The fermentation residuals are de-watered in decanter centrifuges. The phase with high portion of solid matters is supplied to the dryer. After acidification and de-gassing, the liquid phase is evaporated. The concentrate of the evaporation plant is dried together with the solid matters from the decanter. The vapor condensate is further cleaned in a membrane filtration plant or in an alkaline water scrubber, and can then be used as process water. The energy for the plant operation comes from small de-centralized block heating power stations.
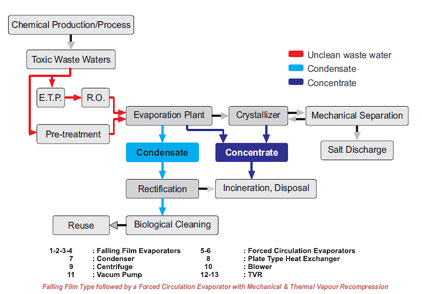